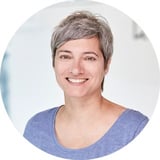
VALUABLE CRAFTSMANSHIP: HAND-KNOTTING RUGS
Carpets in all sizes, patterns and colors are design element and a warming comfort factor in our living space. In particular hand-knotted oriental rugs are currently enjoying new popularity. More and more people wish to go back to more nativeness and naturalness and realize the importance of sustainable products.
That is why also the interest for traditional, high-quality craftsmanship is increasing. Traditional patterns of ancient knotting techniques are a gorgeous eye-catcher und can be easily combined with trendy furniture styles.
Today, there are many possibilities to acquire the beautiful home accessory: for example in the furniture store or online shop, at the carpet dealer or during holidays on the market. Due to modern, automatic production methods and dumping prices of manually produced carpets, the fluffy floor cloths can be bought at bargain prices nowadays.
But a real one of a kind rug can only be hand-crafted. Its production is extremely time-consuming. The fabrication of a handmade carpet needs countless working hours and veritable craftsmanship which shouldn’t be underestimated. To recollect the value of traditional carpet production as an ancient craftsmanship, we will present you in this article the oldest and most labor-intensive way of rug production: Hand-knotting.
Origin of hand knotting rugs
The art of hand knotting rugs probably originates from pre-Christian nomadic people. In the chilly steppes of Central Asia, they produced – besides sheep skins for warming garments – carpets for their tents, to protect them from intruding cold.
Therefore, they wove wool of own goats or sheep to flat fabrics which they attached on the floors and walls of their tents. Thus, already at that time, knotted rugs did not only serve as insulation but, as today, they were also a decorative element.
Craftsmanship with a knotting frame
The first and most simple frames for hand-knotting were made of two wooden beams that were attached in the floor. Between those two beams, the thread was inserted. Those horizontal, folding frames were very practical for itinerant nomads and are still being used today.
Over the centuries, the knotting techniques elaborated and also the frames developed. Vertical knotting frames developed and partially superseded the horizontal ones. In the 16th century, the art of hand-knotting rugs was developed in carpet knotteries of courts of Persian and Indian sovereigns, both regarding artistic and technical aspects. Today, there are many different ways of producing oriental rugs: They are either crafted by single persons (nomads, farmers) or in collaboration of several persons in small ateliers and big manufactures.
The making of a hand-knotted rug
The handcrafting of carpets is very labor-intensive and requires a high degree of accuracy. Hand-knotting a carpet measuring 300 x 400 cm, with a knot count of 500.000 knots per square metre, takes about 600 days. This explains the high price of hand-knotted rugs.
In addition to the knotting frame, a carpet knotter needs further tools like a scissor, a wooden and a metal comb as well as a cutter.
Traditionally, before being able to knot, the lisle that is used for knotting had to be produced. For that purpose, wool of sheep (much earlier also wool of goats) were spun, dyed and dried.
Knotting techniques and knots
Knotting is the process of linking thread, weft and knot, that is being integrated into the basic weave. When knotting the rug, the lisle is bei
ng knotted row after row around the warp that is fixed within the frame. With a comb, the rows of knots and strands of weft are being pressed toge
ther tightly.
As every knot is knotted individually, the most diverse patterns can be created. There are two different knots for hand-knotted oriental rugs, which can also be used in the same carpet: the Persian Senneh knot (also called “asymmetrical knot”) and the Turkish Ghiordes knot (also called “symmetrical knot”). Besides those two knots there are further knots as the Tibetan and the Moroccan knot. These knots, however, are not being used a lot nowadays.
When the rug is finished, it is being washed. This is not only for cleaning purposes: The cleaning process also influences the intensity of the colors and the haptic of the carpet. As soon as the rug is dry again, it is trimmed by a scissor. This way, the length of the pile can be defined, and mistakes can be cut out. Fringes are being affixed and the long sides are being furnished with fringe embroideries.
When the rug is finished, it is being washed. This is not only for cleaning purposes: The cleaning process also influences the intensity of the colors and the haptic of the carpet. As soon as the rug is dry again, it is trimmed by a scissor. This way, the length of the pile can be defined, and mistakes can be cut out. Fringes are being affixed and the long sides are being furnished with fringe embroideries.
The value of hand-knotted rugs
As already mentioned, the density of the knot per surface is determining for the value of a rug. More knots mean more working hours and a higher quality and lifespan of the product. Further, also the used material, the origin of the carpet and its age play a part in the determination of its value.
Besides sheep wool that is used for pile, thread and weft, also cotton is being used quite often for thread and weft. While wool of goat was used for the pile in the past, today it finds use in thread, weft and embroidery. Silk in pile, thread and weft finds use in particularly valuable carpets.
By the way, machine-made carpets can be distinguished from hand-knotted ones on their back side. The best machines for carpet production cannot work in such a precise way that they can exactly imitate a hand-made knot.
- Behind the scene
- technically